Самодельные инструменты-абразивы
Механизировать эту работу в домашних условиях несложно с помощью электродрели или бормашины, закрепив в патроне соответствующий абразив. Но как раз нужного-то подчас под рукой и не оказывается Однако наиболее употребительные можно изготовить своими руками.
Для шлифовки небольших изделий часто достаточно простой наждачной шкурки, намотанной на металлическую державку. Чтобы шкурка не провертывалась, один ее край закрепляется в специальном пропиле Намотку на стержень выполняют различными способами, получая инструмент той или иной формы. В некоторых случаях целесообразно употреблять стержни с кольцевым выступом: он препятствует сползанию листка во время работы.
Из подручных материалов и некоторых отходов удается изготовить и абразивные головки различной формы, предназначенные для обработки и доводки фасонных поверхностей. Формуют головки из абразивного порошка — пылевидных отходов, накапливающихся под заточными устройствами. Их следует осторожно промыть для удаления слишком мелких частиц и пыли обрабатывавшихся материалов. Железные опилки извлекаются магнитом, завернутым в полиэтиленовый пакет: время от времени магнит вынимают, а налипшие на пакет опилки смывают струей воды.
Готовый порошок сушат и просеивают через мелкую металлическую сетку. Затем абразив смешивают со связующим — эпоксидной смолой или силикатным (канцелярский) клеем. Получаемая масса доводится до полного смачивания. Смесь набивается в заранее подготовленные формы, близкие по конфигурации к обрабатываемой поверхности. Материалом для форм послужит и бумажный стаканчик, и фунтик из полиэтиленовой пленки или фольги, и патрончик из картона, пропитанного парафином. В заполнившей их абразивной массе выдавливается углубление или сквозное отверстие под металлическую ножку для крепления в патроне. Такой держатель вклеивается на эпоксидке, а может и запрессовываться в саму массу при формовке. Если готовая рабочая головка не имеет соосности с ножкой, ее следует обточить при вращении грубым абразивом.
Для заточки отрезных дисковых фрез, пильных цепей требуются тонкие диски, которые входили бы между зубьями. Их легко получить, склеив обратными сторонами два листа наждачной шкурки на тканевой основе. Лучше это делать на эпоксидном клее: он пропитает ткань и дополнительно укрепит зерна. На время отвердения смолы пакет кладут под плоский тяжелый предмет.
Такой диск не годится для прорезания узких пазов в твердых материалах — нужны другие, с зернами не только по бокам, но и внутри. Такой инструмент также можно сделать самому.
Например, диск толщиной в один миллиметр получают, пропитав эпоксидкой четыре слоя марли, па каждый из которых через металлическую сетку просеивают абразивный порошок. После составления такого «бутерброда» его помещают между листами полиэтилена (к нему не прилипает эпоксидка) и оставляют под грузом до отвердения смолы. При необходимости так же могут быть покрыты абразивом и наружные плоскости диска. Окончательная форма придается ножницами по металлу. Готовые диски закрепляют на специальных металлических оправках или на обыкновенный болт с отрезанной головкой — с помощью гаек и шайб большего диаметра.
Для окончательной высококачественной или декоративной шлифовки изготовляют •вращающиеся абразивные щетки Сначала вытачивают цилиндрическое основание (бук, дуб) в нем проделывают отверстия под ножку и параллельные пропилы, в которые вставляют смазанные клеем ПВА полоски наждачной шкурки. Если такие работы приходится выполнять часто, основание стоит выточить из металла (дюралюминия) в виде стакана с пропилами, в него помещается резиновый цилиндр с аналогичными пропилами, в которые вставляются лепестки шкурки Остается накинуть на осевой стержень с резьбой шайбу и гайку; при закручивании резиновый цилиндр сдавится. крепко захватив лепестки. При диаметре стакана 35 мм можно установить 16 лепестков.
После тонкой шлифовки иногда требуется отполировать изделие Конечно, здесь незаменим войлочный круг. Однако подойдут и обрезки хлопчатобумажной или шерстяной ткани, прошитой в 6—8 слоев. Такие заготовки надеваются на стержень оправки до получения желаемой общей толщины.
Трубка-сверло для стекла
И, Эдельман делится с читателями одним весьма простым способом сверления отверстий в стекле. Метод привлекателен тем что не требует специальных станков, в то же время позволяя сверлить стекло практически любой толщины. При этом край отверстия может быть максимально приближен к краю стекла; метод позволяет также вырезать кольца и кружки- разного диаметра.
Все это достигается металлической трубкой соответствующего диаметра и порошком абразива Еще потребуется простейший кондуктор лист фанеры с отверстием по диаметру трубки.
Вся операция займет минут пятнадцать в зависимости от толщины стекла. На ровную плоскость укладываем лист картона: на него стекло, а сверху фанерный кондуктор. В его отверстие вводим несколь ко капель воды и тонкий слой наждачного порошка Затем вставляем трубку и поворачиваем ее вправо-влево. Уже через несколько поворотов на поверхности стекла четко обозначается кольцевая бороздка.
По мере углубления трубки и приближения процесса сверления к концу нажим необходимо постепенно ослаблять, чтобы не образовались сколы и трещины с нижней стороны стекла.
Сварщик-авторучка
Такая «авторучка» пригодится всем, кто любит мастерить, пишет И. Симонович.
Обычная пайка занимает много времени, требует затрат большого количества электроэнергии. Поэтому ее лучше заменить сваркой, при которой не нужны ни лужение проводов ни добавка третника.
С «авторучки» снимаете колпачок, дотрагиваетесь до свариваемого узла «пером», нажимаете так, чтобы оно слегка зашло внутрь ручки, и сварка готова. Можно приступить к следующему узлу.
Сделать такую «авторучку» очень просто. Надо запастись следующими материалами: пластмассовым корпусом и колпачками от негодной авторучки, обрезком медной трубки диаметром немного меньше, чем диаметр корпуса и длиной 75 мм, куском латунной проволоки диаметром 1,2 мм. из которой следует скрутить пружину, медным или стальным стержнем диаметром 5 мм и длиной 17 мм, кусочком медной трубочки с внутренним диаметром 5 мм и дли ной 20 мм. угольным сердечником от батарейки карманного фонаря и, наконец, изоляционной трубкой, какой обычно пользуются для монтажа радиоаппаратуры.
Круглым напильником сточите внутреннюю резьбу корпуса авторучки и зачистите это место мелким наждаком. В торце маленького колпачка просверлите отверстие для проводов. В большой трубке сделайте прорезь и впаяйте в нее латунною пружинку. С одного конца стержня сточите полови ну сечения и прорежьте ее ножовкой вдоль на 10 мм. В эту прорезь впаяйте изолированный провод. С противоположного конца стержня просверлите отверстие для крепления захвата.
После того как захват закрепите на стержне шпилькой, натяните изоляционную трубку В захват вставьте угольный электрод Теперь все готовые детали можно вмонтировать в корпус авторучки и заклинить в меньшем отверстии пластмассовыми клинышками. Навинтите малый колпачок.
Сердечник трансформатора изготовьте из трансформаторного железа сечением 40X70 мм Соленоид намотайте в два слоя на текстолитовом каркасе (диаметром 16 мм длиной 40 мм) и вмонтируйте под общий кожух с трансформатором.
Вся установка рассчитана на питание от сети переменного тока в 220 или 127 В.
Переключатель и выпущенные из вторичной обмотки отводы дают возможность регулировать режим сварки от 3,6 до 10 В.
Необходимое напряжение подбирается в зависимости от диаметра свариваемых проводов по таблице.
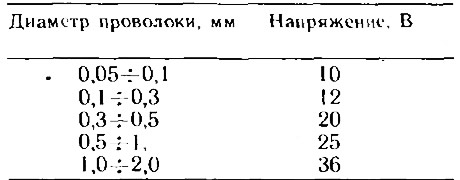
Если «перо» дотронулось до свариваемых проводов и вы продолжаете нажимать на них, «перо» подается в середину корпуса и цепь замыкается угольным электродом Плохой контакт в этом месте создает дугу, которая и сваривает провода.
Журнал «САМ» №5, 1993 год